武田薬品は5日、グローバルプログラム「Factory of the Future」の一環として進める製造デジタルトランスフォーメーション(DX)の取り組みにについて発表した。
Factory of the Future は、同社の全製造拠点が、それぞれの機能や製造する医薬品に基づき作成するロードマップに従って、デジタル教育の強化と変革の推進(Organizational Learning & Change Management)、デジタルと自動化 (Digital & Automation)、生産性や効率性の追求(Enterprise Excellence)の3つの側面から変革を行うプログラムだ。
製造DXの取り組みにおいては、AI、デジタルツイン、ビッグデータ解析などの先進技術を活用し、全世界の製造拠点におけるイノベーションの推進を加速する。これにより、医薬品の品質と安定供給を強化し、患者のニーズに迅速かつ柔軟に応えられる体制を構築する。
同社では、世界中に 25 以上ある製造拠点の全てにおいて、「すべての患者さん(Patient)」、「ともに働く仲間(People)」、「いのちを育む地球(Planet)」のためにデータとデジタルの力でイノベーションを起こすという同社の約束を実現すべく、製造DXを推進している。
各拠点で成果を上げたベストプラクティスのノウハウをグローバル統一プラットフォーム「Global Market Place」上に集約し、どの拠点でも導入できるようにし、拠点間で相互交換・横展開している。これにより新たなソリューション開発にかかる工数や投資の重複を避けることにもつなげている。
「すべての患者さんのために(Patient)」では、予測型工場として、保守およびビジネス価値創造の両面から、医薬品の品質保証と安定供給をさらに強固にしている。トラブルを未然に防ぐ保守として予知保全(Predictive Maintenance)を実現。設備から収集される時々刻々のデータを、クラウド上に実装された異常検知モデルに接続し、リアルタイムに異常検知を行うことで突発故障を未然に防ぐ。
さらに、機器の故障などに起因する逸脱の回避を行う。これにより、遅滞のない製造の実現を目指すとともに、逸脱が起きた場合に発生する原因調査、影響範囲特定、是正処置の立案、必要な変更の実施など、膨大な時間と工数が伴う対応の発生を未然に防ぐ。
また、ビジネス価値の創造として、収量の改善(Yield Improvement)を目指す。製造設備各所に取り付けたセンサーから得られるビッグデータを活用し、予測モデルを開発して、製造工程における改善機会を特定する。
製造に関する膨大なデータをリアルタイムに分析できるマルチエシェロン在庫最適化(MEIO)プログラムを導入し、拠点や国を超えた当社の供給ネットワーク全体に渡って在庫量を最適化する取り組みを行っている。
MEIOでは、デマンドパターンや製造リードタイム、供給変動、コストやサービスレベルを考慮することで、市場の変化や予期せぬ混乱に対して素早く順応することができるようになり、同社の医薬品を必要とする患者のために、より迅速で柔軟な供給体制の構築を図る。
将来的には機械学習の導入により、サプライチェーンのさらなる自動化が見込まれており、これにより自律的な運営が可能になるものと期待される。
「ともに働く仲間のために(People)」にでは、デジタルと人の連携で、生産性と働き方の改善を行っている。GMP(医薬品の製造管理及び品質管理の基準)を厳格に順守する必要がある医薬品の製造現場では、高度な無菌性環境下やこれまで使用したことのない設備を用いた新製造ラインでの初回製造(Process Performance Qualification: PPQ)など、オペレーターのトレーニングを実施することが容易ではなく、習得に時間がかかる状況がある。
こうした中、トレーニングに VR(仮想現実)や AR(拡張現実)を活用することで、実際の作業環境にバーチャルで没入して学べるようにしたり、実空間上にデバイスやインストラクションを浮かび上がらせてトレーニングを行ったりすることが可能になり、従来と比較して、より少ない人数・工数でオペレーターが実践的、効率的、かつスピード感を持ってのトレーニングを実現している。
「いのちを育む地球のために(Planet)」では、製造設備から収集したビッグデータの活用で環境への負荷や影響を見える化し、オペレーションや設備の最適化を通じて環境負荷低減を行っている。
「すべての患者さん(Patient)」、「ともに働く仲間(People)」、「いのちを育む地球(Planet)」の主な具体的取組は、次の通り。
【すべての患者さんのために(Patient)】
◆IoTを用いた予知保全(大阪工場)
武田薬品の複数の主要製品の製造では複雑な機器である凍結乾燥機を用いており、故障などのトラブルが発生すると基準通りの製品を製造することができなくなるリスクもある。
大阪工場では2021年度に凍結乾燥機の一部として使用されている真空ポンプなどの回転機器に振動センサーを導入し、状態監視を開始した。2022年10月にはドライ真空ポンプの振動値が基準内での上限に近づき始めたことが測定データから確認されたため、生産計画に影響を与えない直近のメンテナンスタイミングで軸受けの確認をしたところ、摩耗していることが分かった。
新品の軸受けに交換した結果、振動値が正常域まで低下したことが確認されている。振動センサーを用いた回転機器の集中監視が機器の健康状態をタイムリーに把握し、機器トラブルの予防、ひいては医薬品の安定供給に寄与することが示された好事例となる。
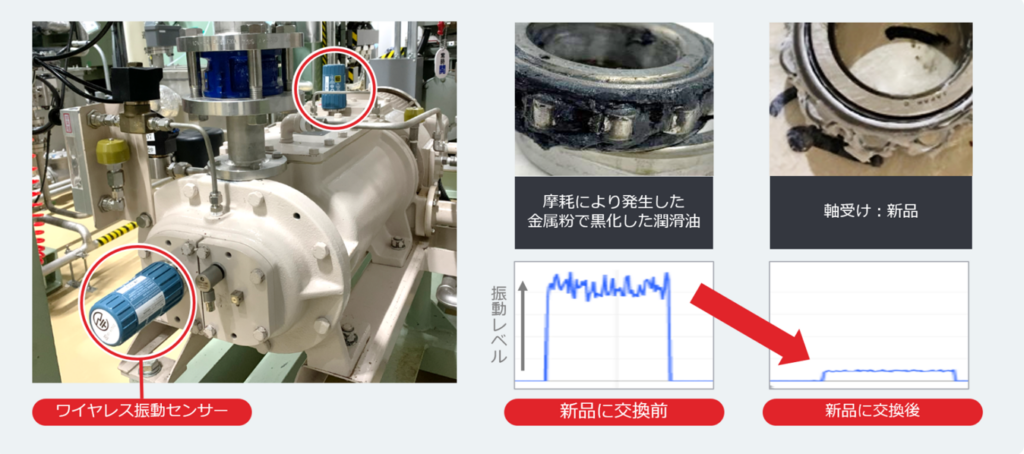
◆ビッグデータを活用した収量改善(光工場)
武田薬品の光工場における原薬製造には200種類以上の製造パラメータが関与している。従来はこれらをラボ実験で個別に検証し収量向上を試みていたが、パラメータ数が多いため、収量に影響を与える要因の特定が困難であった。
同取り組みでは、製造実行システムやラボ情報管理システムなどからの製造データや品質データ、さらには気象データなどの外部データをクラウド環境で統合し、多変量解析や機械学習を利用してより高精度な収量予測モデルを構築した。
このモデルの出力結果と、これまで現場で蓄積してきた知見を融合することで収量に影響を与える重要なパラメータを十数個まで絞り込み、その中でも冷却時間が特に重要であることを特定した。
この分析結果を受けて冷却水バルブの開度を最適化するように現場の作業手順を標準化することにより、収量の4.0 % 増加を達成している。これにより、同じ原料からより多くの患者への製品供給が可能になる。

◆デジタルツインによる収量改善(スイス・ヌーシャテル工場)
ヌーシャテル工場では、血漿分画製剤の製造において、不純物を除去する重要な工程で回収率の低下による生産性の課題があり、結果として患者に供給できる医薬品の最大量を達成できていなかった。
そこで、2022年度よりデジタルツインを活用した生産プロセスの分析を開始した。同ツールは、企業データバックボーン(EDB)から収集されるデータを用いて、生産ラインのボトルネックや非効率的なプロセスを特定し、改善のための実証済みのソリューションを提供している。
特に、低回収率の課題に対しては、デジタルツインを使って根本原因を特定し、機械学習モデルを活用してプロセス全体を最適化した。その結果、2023年初頭には、不純物除去プロセスでの収率が大幅に改善され、生産性が向上した。これにより製造の中断が減少し、より多くの患者への医薬品供給が可能になった。
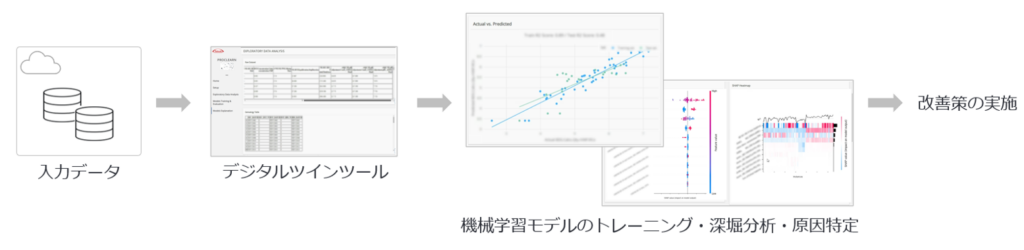
【ともに働く仲間のために(People)】
◆AR技術を用いたトレーニングで新製造施設のPPQの成功に寄与(光工場)
光工場では、主要製品の新製造施設の初回生産(Process Performance Qualification: PPQ)をAR技術の活用で成功裏に完了した。PPQは新設備の製造方法や規格が効果的に機能するかを確認する重要なステップだ。
光工場に設置された新製造ラインは「シングルユース機器」を用いて高い製品品質を保証しているが、操作手順を必要とするもので、かつ、当時の現場オペレーターにとっては使用経験のないものであった。
AR技術を用いた機器操作トレーニングにより、オペレーターはオフィスでも製造作業を仮想体験でき、より直観的に操作手順を学ぶことが出来るようになった。この取り組みにより、シングルユース機器を使った初回生産での作業ミスはゼロとなり、高品質な製品の安定供給が実現した。
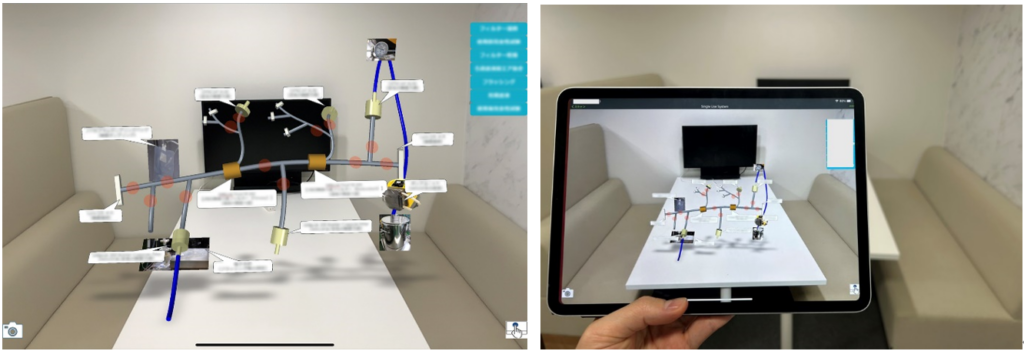
【いのちを育む地球のために(Planet)】
◆データとデジタルを活用した効率的な働き方と環境負荷低減の実現(大阪工場、天津工場)
武田薬品の大阪工場では、製造設備の洗浄に使用する蒸留水の不足により、設備の停止や生産遅延が発生していた。
そこで、リアルタイム情報管理システムを用いて各設備の蒸留水使用量を即時的に可視化・分析できる仕組みを構築した。また、手動での機器洗浄における蒸留水使用量のデータ収集のため、配管にセンサーを設置し、クラウド上でデータを可視化した。
これに基づき、設備・プロセス・使用時間帯の最適化やオペレーターの作業の標準化を行った結果、年間で45万L以上の蒸留水を削減した。これにより、200万l以上の上水と7900m³以上の都市ガスの削減にもつながり、環境負荷の低減と従業員のデータ活用意識の向上を実現した。
同様に中国・天津工場でも、リアルタイムデータを活用した上水利用の可視化による従来比約20%の使用量削減の好事例が確認されている。
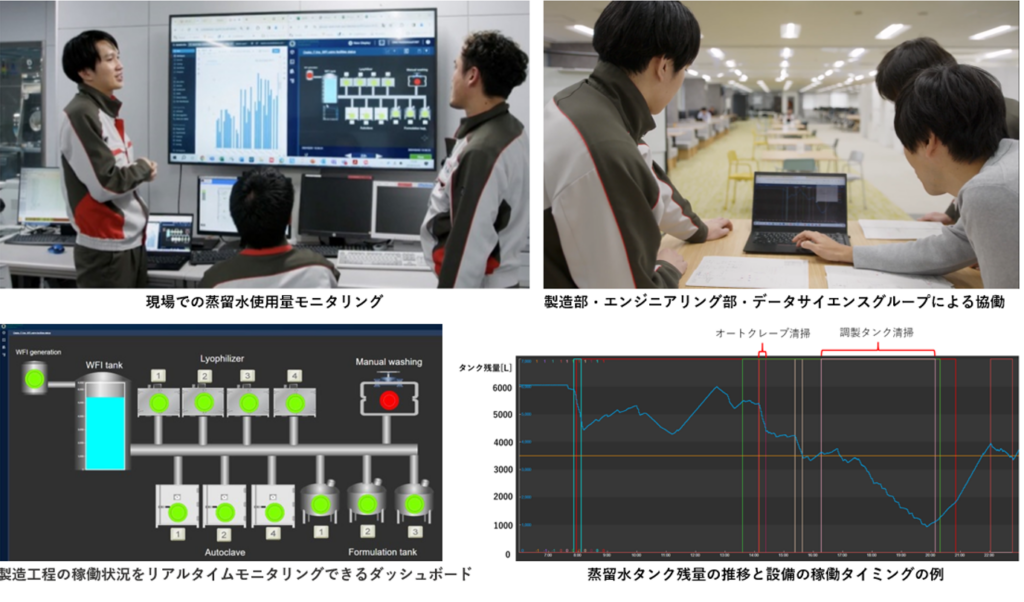
◆グレッグ・ティモンズ武田薬品グローバルマニュファクチャリング&サプライ ジャパン ヘッドのコメント
急速に変化する世界の中で、ヘルスケア課題に持続的に取り組むために、我々は絶えずイノベーションを追求しなければならない。
当社は、データサイエンスとデジタル技術への投資を加速させ、自動化、AI 開発と標準化、データの統合と民主化、人材開発、予測能力、そして革新的なコラボレーションとガバナンスを強化している。
AIや自動化は、人(従業員)がより価値を創造する業務に注力することを支援するものである。そのため、従業員のデジタル教育に力を入れデータ活用意識の向上を図ることで、製造プロセスやオペレーションのあらゆる側面で DX に取り組み、患者が必要とする医薬品のより迅速な安定供給に努めていく